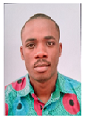
Chukuwgozie Jekwu Ejeh
Khalifa University of Science and Technology, Abu Dhabi, United Arab Emirate
Title: Thermo-elastic Deformation of Carbon Fiber Reinforced Polymer Composite Shell under Unsteady Deposited Beam Heat Power using Finite Element Analysis
Biography
Biography: Chukuwgozie Jekwu Ejeh
Abstract
Thermal stress on engineering materials is one of the major cause for failure in engineering structures. Limited work has focused on investigating the effect of increasing heat-induced thermal stresses to the yield strength of carbon fiber reinforced polymer composite material. Layer-wise approach through finite element analysis (FEA) was used to facilitate achievement of the objective function. This paper aims at investigating the thermo-elastic behaviour of a composite shell under varying heat power measured in Watt. Furthermore, coupling the thermal and mechanical system, and the application of a non-linear solver created an interaction between the boundary condition and material structure. The deposited beam heat power was modelled and implemented through heat transfer in shells physics with COMSOL Multiphysics software. The heat power intensity was varied between 10 to 100W, and further increased to 200W using other case composite formulations to test their structural integrity under similar scenario. The beam was focused at the centre of the laminate (= 0.15m) composed of six (6) layers arranged in different stacking sequences. Post-processed results depicts that the material deformed non-linearly along fiber direction. The deformation was more pronounced along the fiber direction compared to in-shear mid-plane of the laminate. One information that can be obtain from the result is the ability for composite material to regain its original shape gradually whilst distributing the stress evenly across other parts of the laminate. Using carbon fiber was doped with silicon carbide (SiC), and using resin bonded glass fiber, yielded different results. An enhanced thermo-elastic behaviour of the material was achieved with carbon fiber reinforced silicon carbide matrix. It was observed to absorb the thermally-induced stress and distribute evenly across other sections of the composite shell. Hence, regained its original shape faster that its counterpart. Notwithstanding, the FE model was validated with experiments.